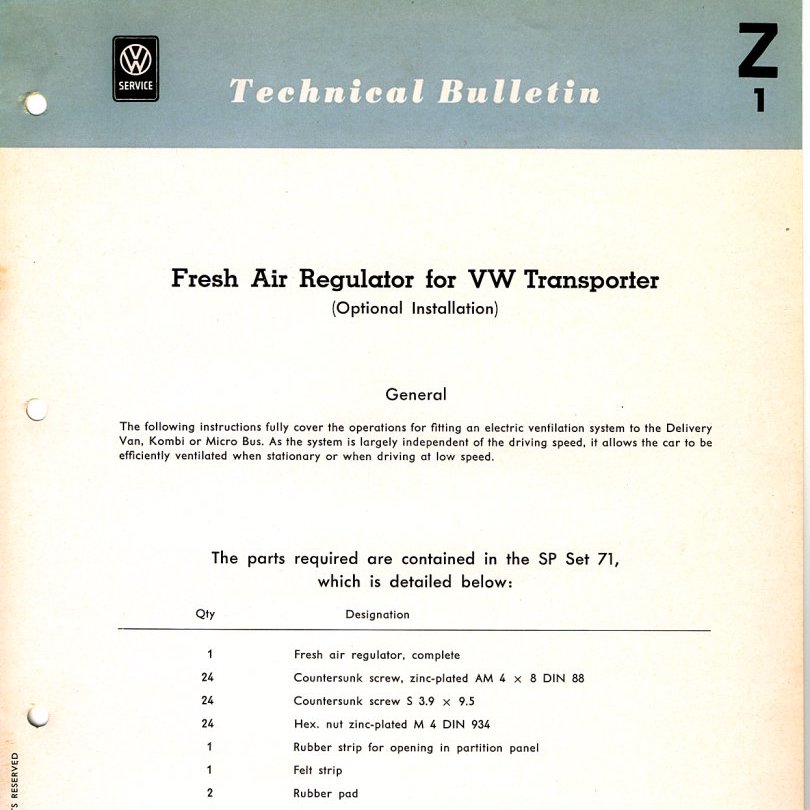
Technical Service Bulletins zijn berichten van de fabrikant aan de dealers waarin ze uitleggen hoe je bepaalde problemen kunt/moet aanpakken. Je moet het niet verwarren met een terugroep actie.
Deze acties zijn vaak nodig om een risico weg te halen. Dit zijn meer nieuwsberichten met voortschrijdend inzicht om bepaalde zaken op te lossen. Hier een overzicht van deze bulletins van een Amerikaanse bron.
AFFECTED MODEL | MODEL YEARS | ORDER NUMBER | AFFECTED COMPONENT | SUBJECT |
---|---|---|---|---|
Vanagon | 1986 | 87-N02 | Climate Control | Don’t Blow Your Top – High Pressure Discharge Hose/ Remove Damper |
Vanagon | 1986-87 | 87-N04 | Fuel System | Vanagon Surging/Stalling – Adjusting Throttle Switches |
1.9 liter Vanagon | 1982-85 | 87-N05 | Engine | Easy Does It – Cross-over Water Pipe |
Vanagon | ALL | 87-N06 | General | Vanagon “Dust Buster” air filter – Heavy Duty Air Filte |
Vanagon | 1987 | 87-N08 | Fuel System | Basic Digifant Assumptions – Digifant Management System |
Vanagon | 1986-88 | 88-N07 | Cooling System | Coolant Loop – Transmission Removal |
Vanagon | 1988 | 88-N08 | Fuel System | “Terminal Illness” (Idle Stabilizer System Changes) |
Vanagon | ALL | 88-N09 | Fuel Engine | Throttle Switch Adjustment Ti Remanufactured Engine |
Vanagon | ALL | 10-87-02 | Engine | Remanufactured Engine Identification |
Vanagon Water-boxer | ALL | 15-90-T0 | 1 Engine | Cylinder Head Re-Seal (1.9L and 2.1L) |
Vanagon | 1983-85 | 17-87-04 | Engine | Oil Leak from Rear – Oil pump gaskets |
Vanagon waterboxer | ALL | 17-87-05 | Engine | Oil cooler seal leaks in extreme cold |
Water-cooled Vanagon | 1983-85 | 19-87-02 | Engine | Coolant leaking and/or noise from rear water pump |
Water-cooled Vanagon | 1983-85 | 19-87-03 | Engine | Carpet wet by rear seat – Heat Exchanger T-piece leakin |
All w/ Gasoline Engines | ALL | 20-20-90 T01 | Fuel System | Improved Fuel Additive ZVW 239 003 |
Vanagon | ALL | 20-90-01 | Fuel System | P.I. 2082 – Accelerator Cable Change |
All w/ Fuel Injection | ALL | 20-90-02 | Fuel System | Gasoline Containing Detergent |
Vanagon | 1983-90 | 24-24-90 T01 | Fuel System | Rough Idle, Engine Stalls – Tow In |
Vanagon | From 1986 on | 24-89-04 | Fuel System | Digifant I: Fuel Injection System Cleaning and Intake Valve Decarbonization |
Vanagon w/ Digijet Injection | ALL | 24-90-03 | Fuel System | Throttle Body – Replacement |
Vanagon w/ Digifant injection | 1986-91 | 24-92-01 | Engine | Intermittent Misfire |
Vanagon water-Boxer | 1983-91 | 24-92-02 | Engine | Driveability Complaints |
Vanagon w/ Digifant Injection | 1986-91 | 24-92-01 | Electrical System | Vanagon Intermittent Misfire |
ALL | ALL | 27-87-03 | Engine | Cruise Control does not work Vacuum loss |
Water-cooled Vanagon, Diesel Vanagon | Thru Model Year 1985 | 27-87-04 | Electric | Alternator Mounting Bolt loose/broken |
All Models | All Years | 28-87-04 | Ignition System | Rough idle or misfiring during partial load |
Vanagon | From 1986 | 28-90-01 | Ignition System | Vehicle Does Not Start, Ignition Miss |
Vanagon w/ Manual Transmission | ALL | 30-89-01 | Manual Trans. | Clutch Disc – Installing |
Vanagon w/ 091/1 Transmission | ALL | 34-89-02 | Manual Trans. | Position of Boot on Shift Rod Bushing |
Vanagon w/ Manual Transmission | ALL | 34-89-03 | Manual Trans. | Revised Shift Lever Bearing |
Vanagon | ALL | 40-88-01 | Suspension Wheels | Upper Control Arm Bushings, Checking |
Vanagon | ALL | 42-87-01 | Suspension Wheels | Knocking noise from rear – CV Joint |
Vanagon Syncro | ALL | 42-89-01 | Suspension Wheels | Coil Spring, Installation Position |
Vanagon | 1983-85 | 55-87-01 | Body Exterior | Push Button Operation Difficult – Rear Lid Latch |
Vanagon Wolfsburg | 1987 | 63-87-01 | Body Exterior | Front Bumper/Spoiler – Removing/Installing |
Vanagon | From 3/86 on | 64-86-06 | Body Exterior | Power Operated Window Motor – Removing/Installing |
Vanagon | From 1986 on | 66-87-01 | Body Exterior | Outside Mirrors (Electric) – Increasing Mirror Glass Adjustment Range |
Vanagon | ALL | 66-87-03 | Body Exterior | Outside Mirrors, Electric Mirror Assembly – Removing/ Intalling |
Vanagon Wolfsburg | 1984-85 | 68-84-01 | Body Interior | Rear Bench Seat Belts |
Vanagon Camper/Multivan | 1980-89 | 68-91-02 | Seat Belts | Automatic Rear 3-Point Seat Belt, Retrofit Installation |
Vanagon w/center seat except Camper/Multivan | 1980-89 | 68-91-04 | Seat Belts | Automatic 3-Point Left Center Seat Belt, Retrofit Installation |
Vanagon | 1983-85 | 70-87-02 | Body Interior | Front Carpet Seam Gap |
Vanagon | From 1980 on | 76-89-01 | Body Interior | Refrigerator Air Supply Modification (Dometic 182 Models) |
Water-cooled Vanagon | 1983-85 | 80-87-01 | Climate Control | Carpet Wet by Rear Seat – Heat Exchanger Bleeder Screw Broken |
Vanagon w/ A/C | ALL | 87-84-06 | Climate Control | A/C Evaporator Blower Motor – Installation of Reinforcement Plate |
Vanagon | 1984-85 | 87-85-01 | Climate Control | Factory Installed Air Conditioner – Replacement of A/C Refrigerant Hose Mounting |
Water-Cooled Vanagon | From 1986 on | 87-87-02 | Climate Control | Water out of A/C Vents – A/C on |
Vanagon w/ A/C | From 1986 on | 87-87-04 | Climate Control | Remove Noise Damper from A/C Refrigerant High Pressure Hose |
Vanagon w/ A/C | 1986-89 | 87-89-01 | Climate Control | Evaporator Housing – Change |
Vanagon Van, Camper Waterboxer | ALL | 87-90-01 | Climate Control | A/C Evaporator – Water Leaking |
Vanagon | ALL | 90-86-02 | Electrical System | Non-Interchangeable Cigarette Lighter |
Vanagon except syncro | ALL | 90-90-01 | Electrical System | Speedometer Noises (Except Syncro) |
Vanagon | ALL | 90-90-02 | Electrical System | Instrument Indicator Lights Malfunction |
Vanagon Water-Cooled | ALL | 97-87-05 | Electrical System | Engine Cranks Too Slowly or Won’t Crank – Battery Cable |
ALL Water-cooled | ALL | 90-92-03 | Electrical System | Coolant Indicator LED is Flashing at Normal Temperatures |
ALL Watercooled | ALL | 90-87-03 | Electrical System | Coolant Temperature Gauge Light flashes intermittently / continuously |
ALL Hydraulic Valves | ALL | 88-N04 | Engine | Stalling when cold, or zero compression |
En hieronder een lijst met beschrijvingen er bij.
======================================================================== Import Service, Jan '89, Vol 2, No1 vanagon A/C hose damper "1986 Vanagons up to VIN 25HH003407 had a damper/restrictor installed in the high side hose coming from the air compressor. Occasionally, these dampers would cause compressor head pressures high enough to actually blow the compressor head seal. The tube in question is about 17 inches long. Make sure you remove all of it and discard it if you find it still in place, especially when replacing a compressor seal that was blown by excessive head pressure." From: "Dan Houg"======================================================================== from Technical Newsletter, 88-N04 ........................................................................ Volkswagen Technical Newsletter 88-N04 High Pressure, Low Performance A Volkswagen that stalls when the engine is cold or after driving a few hundred feet could be suffering from an air/fuel imbalance. It could also have a bad oil pump. That's right, oil pump! If the same engine has zero compression, the chances are even greater than the oil pump is to blame. If the oil pressure relief valve sticks, oil pressure could rise to over 200 psi when you accelerate to drive off. With pressure that high, the hydraulic valve lifters will overextend themselves, causing the valves to hang open. After the engine warms up, the car will probably run great the rest of the day. So check the oil pressure when you've tried everything else to solve a stalling problem ... believe it or not! ======================================================================= from Service Bulletins, Model Year 1990 ........................................................................ Technical Information Group: 20 Number: 90-01 Date: March 31, 1990 Subject: P.I. 2082 - Accelerator cable change Model(s): Vanagon, all Model Years A modified accelerator cable has been introduced in production, as of VIN: 25 JH 062 158. The modified cable is available through the Parts Deivision. Although the part number remains the same, the improved cable can be identified by a white plastic sheath enclosing the length of the braided cable. This sheath protects the braided cable from outside elements. When repairs are necessary to the accelerator, ensure the following: * The boots that cover the ends of the cable housing are installed and not damaged. Replace if necessary. * Check the hose that joins the housings. If not intact, replace it and install hose clamps on both ends. * Install improved accelerator cable. ................................ end .................................. part numbers for reference: check with the Accelerator cable: manual trans - 251-721-555 Q Parts Dept. to auto trans - 251-721-555 E make sure these Rubber boot (rear/engine): 251-723-580 are correct. Rubber boot (front/pedal): 251-723-580 ........................................................................ Technical Information Group: 28 Number: 90-01 Date: March 31, 1990 Subject: Vehicle does not start, ignition miss Model(s): Vanagon, from 1986 Model Year If the engine does not start or in case of ignition related engine miss, check the ignition coil for bitumen leakage. Bitumen leakage may be caused by overheating of the ignition coil which may occur when the engine runs for a prolonged period of time at idle. Replace the standard grey labeled ignition coil with green labeled coil Part No. 211 905 115 D. The green labeled coil was installed into production as of 1/89. VIN: 25HG 06 5838. ***************************************************************** * CAUTION * * Part numbers are for reference only. Always check with your * * Parts Department for latest information. * **************************************************************** ======================================================================== from Service Bulletins, Model Year 1992 ........................................................................ Technical Bulletin Group: 24 Number: 92-01 Date: February 29, 1992 Subject: Vanagon Intermittent Misfire Model(s): All Vanagon Digifant Fuel Injection Engines CONDITION After driving for 1/2 to 2 hours at a constant speed, vehicle experiences lack of power, cuts-out or stalls, often accompanied by bucking or jerking of the vehicle. In ALL cases, the vehicle will restart immediately. This symptom may not re-occur for several weeks/months. Inspection by the dealer results in nothing conclusive. Some air-flow meters may experience a vibration resonance of the metering potentiometer wiper during extended constant driving. This resonance causes the air-flow meter to supply an intermittent signal to the Digifant ECU. The ECU will then default to a "no-load" condition and reduce the injection time. SERVICE Harness, Part No. 025 906 302, is available to resolve this condition. * remove electrical connector from air flow sensor (see Figure 24-174) * install converter assembly, Part No. 025 906 302, between harness and air flow sensor NOTE If customer complaints persist after performing the above repair, contact your Zone Product Support Specialist (TSM in Canada). ***************************************************************** * CAUTION * * Part numbers are for reference only. Always check with your * * Parts Department for latest information. * **************************************************************** ........................... end ...................................... harness costs about $100! very simple to install. takes about three minutes maximum. the new harness fits between the old harness and the silver air-flow meter box attached to the air cleaner box. remove the silver clip, wiggle out the big wiring connector (from the side of the air-flow meter), connect the proper end of the new harness to the big big wiring connector you just wiggled out, put the new clip into the new connection; then take the other end of the new harness and plug it into the air-flow meter connection. put the silver clip back. and you are done. ======================================================================= from Service Bulletins, Model Year 1992 ...................................................................... Technical Bulletin Group: 24 Number: 92-02 Date: April 30, 1992 Subject: Vanagon Driveability Complaints Model(s): All Water Cooled Engine Vanagons SUPERCEDES TECHNICAL BULLETIN 24-92-01 (February 29, 1992) CONDITION After driving for an extended period of time at a constant speed, the vehicle may, on occasion, experience a deterioration of performance which may be accompanied by a hestiation or surging. In many cases, after turning off the engine and subsequent re-start or without having taken any action, the symptoms disappear. These symptoms may not recur for several weeks or months. SERVICE To resolve this condition, wire harness Part No. 025 906 302, should be installed. This harness provides improved signal voltage stablization. * remove electrical connector from air flow sensor * install wire harness, Part No. 025 906 302, between main harness connetion and air flow sensor connection. ***************************************************************** * CAUTION * * Part numbers are for reference only. Always check with your * * Parts Department for latest information. * **************************************************************** NOTE When troubleshooting this system and performing continuity checks, the following should be noted. Due to active components in the wire harness, Part No. 025 906 302, there is not continuity between pin two of the connectors. The following chart on page 2 lists the resistence of each circuit. --------------------------------------------- Terminal Approximate Number Resistance --------------------------------------------- 1 Zero Ohms 2 Greater than 1 Meg. Ohms 3 Zero Ohms 4 Zero Ohms 5 Zero Ohms NOTE If customer complaints persist after performing the above repair, contact your Zone Product Support Specialist for assistance. ........................... end ...................................... harness costs about $100! very simple to install. takes about three minutes maximum. the new harness fits between the old harness and the silver air-flow meter box attached to the air cleaner box. remove the silver clip, wiggle out the big wiring connector (from the side of the air-flow meter), connect the proper end of the new harness to the big big wiring connector you just wiggled out, put the new clip into the new connection; then take the other end of the new harness and plug it into the air-flow meter connection. put the silver clip back. and you are done. ======================================================================= IMPORT SERVICE MAGAZINE July '93 Vol. 6 No. 8 Subject: more 'Ghost harness' info After driving for an extended period of time at a constant speed, some water cooled Vanagon engines may loose performance or hesitate and surge. In many cases, the symptoms will disappear after turning off the engine and restarting. After that, the symptoms may not reoccur for several weeks or months. A new wiring harness (P/N 025 906 302) is available to correct this problem. The new harness provides better signal voltage stabilization than the old harness it is designed to replace. To install the new harness, remove the air flow sensor harness connector. Install the new harness between the main harness connector and the air flow sensor connector. There are active components in the new wiring harness. For this reason, there is no continuity between terminal number 2 at one of the harness connectors and terminal 2 in the harness connector at the other end of the new harness. This is normal and should not be considered a fault. All other connector terminals should have 0 ohms resistance from one harness connector to its mate in the connector at the other end of the harness. Keep this in mind when troubleshooting this system and performing continuity checks. From: "Dan Houg" ======================================================================== from Service Bulletins, Model Year 1990 ........................................................................ Technical Bulletin Group: 24 Number: 24-90 T01 Date: May 31, 1990 Subject: Rough Idle, Engine Stalls - Tow in Model(s): 1983-1990 Model Years The clamp for the air intake boot to air flow meter/throttle body may yield tension and could cause a vacuum leak. This may create a lean running condition resulting in the engine to idle rough and in severe cases stall while idling. Installation of Boot Clamp Part Number 191 129 647 will correct this condition. ======================================================================== from Service Bulletins, Model Year 1987 ........................................................................ VW Technical Information Group 42, Number 87-01 Date: August 5, 1987 Model(s): Vanagon, all model years Subject: Knocking Noise from rear - CV Joint A noisy CV joint could be caused by hardened and dried lubricant. * Disassemble and inspect all joints, repack serviceable joints using new high temperature grease Part Number G 000 603. * Replace worn CV joints using Kit Number 251 598 101. This joint has a larger diameter ball bearing (from 19.05mm to 20.0mm) for longer wear. Pack the replacement joint using the new high temperature grease supplied with the kit. Production Change: CV joints with increased bearing diameter installed as of Dec. 1984, VIN 25 FH 055 865 New high temperture grease in use as of Oct. 1986, VIN 25 HH 037 577 ======================================================================== from Service Bulletins, Model Year 1987 ........................................................................ VW Technical Information Group 80, Number 87-01 Date: July 31, 1987 Model(s): Water-cooled Vanagons, 1983-1985 Subject: Carpet wet by rear seat - heat exchanger bleeder screw broken The plastic bleeder screw for the rear heat exchanger may be broken due to seal swelling. * Replace with an improved metal bleeder screw, Part number N 902 061 01. and new gasket, Part number 861 819 037. Production Change: Metal bleeder screw installed as of: December 1984, VIN: 25 FM 050 887 ------------------------------------ as of 1995.04.04, this part number N 902 061 01 was invalid. the newer part number for the Bleeder Screw, as seen on the 1993 Microfiche for Vanagons 1983-1985 and Vanagons 1986-1991 is 861-819-039. the gasket number is still the same. BUT the new Bleeder Screw seems to be plastic again, not metal. in fact, two reliable parts people have said that there were never any "metal" bleeder screws ... only plastic. so apparently this tech info is wrong. but a new bleeder screw might solve the leaking. ......................................................................... VW Technical Information Group 19, Number 87-03 Date: December 21, 1987 Model(s): Vanagon, Water-cooled, model years 1983-1985 Subject: Carpet wet by rear seat - heat exchanger T-piece leaking A coolant leak in the rear heat exchanger area may be due to poor hose fit at the metal T-piece which connects the fee hose to the main coolant hose. An imporved, white plastic T-piece with slightly larger diameter is available to correct this condition: * Replace metal T-piece with white plastic version, Part number 253-265-543A * Remove flow restrictor from inlet fitting of heater valve. Production Change: Improved T-piece installed as of Nov. 1984, VIN 25 FH 037 898. ======================================================================= from Service Bulletins, Model Year 1987 ....................................................................... Technical Information Group: 17 Number: 87-05 Date: October 29, 1987 Subject: Oil Cooler seal leaks in extreme cold Model(s): Vanagon waterboxer, all Model Years Extreme cold weather can harden and split the seal between the engine block and the oil cooler thus creating an oil leak: * An improved cold-restistant seal was installed in production as of 02/87. * The new seal can be identified by its silver-grey appearance and is available through your parts department, Part No. N 901 814.02. ======================================================================= from Service Bulletins, Model Year 1985 ....................................................................... Technical Information Group 87, Number 89-01, August 31, 1989 Model(s): Vanagon with A/C, model years 1986-1989 Subject: Evaporator Housing - change Starting April 1988, a running change was made to the evaporator housing and introduced into production. To prevent cracking, the body attachment points have been relocated. Evaporator housings are now available through the parts depot and come as a multiple supersession with the following items: 1 evaporator housing (color coded) 2 mounting brackets 2 shims (color coded) 6 rivets 6 body plugs (color coded) 6 bolts INSTALLING - disconnect battery - remove front A/C control assembly and center vents - remove both rear side covers at C-pillars - remove both outside vent covers - remove relay assembly from left C-pillar adn all tie wraps holding A/C lines - remove evaporator housing fasteners and lower housing NOTE Discharging the A/C system is NOT required due to the length of the evaporator hoses. A cherry picker with a protective cover helps in lowering the evaporator housing. - bolt brackets to new evaporator housing and lift into postion - with the evaporator firmly positioned against the roof, work through the speaker holes, mark location of new bracket attachment points approximately 40 mm (1.575 in.) above the original holes - lower evaporator housing, center punch and drill holes to accomodate rivets NOTE Rivets can be installed using Kent-Moore tool #M-39010 - install original covers on bolt heads - install remaining components Labor Operation Number: 8760-31-0 Suggested Repair Time: 280 t.u. ======================================================================= from Service Bulletins, Model Year 1990 ....................................................................... Technical Information Group: 87 Number: 90-01 Date: March 31, 1990 Subject: A/C Evaporator - water leaking Model(s): Vanagon/Vanagon Camper Waterboxer, all Model Years Water may come out of A/C vents if the evaporator drain tray does not drain properly. This may be caused by: * A missing or clogged drain valve. A drain valve must be installed on the drain hose to prevent water from being drawn back into the evaporator housing via vacuum created by the blower motors. 1. For 1/2" o/d hose, use drain valve Part No. 253 260 180 2. For 3/8" o/d hose, use drain valve Part No. 431 260 155 Clogged drain valves should be cleaned of all foreign matter and must be reinstalled. A water drain valve has been installed in production as of 5/88. VIN 25JH 09 3520 25JG 09 5871 * Make sure drain hoses are properly routed without kinks or positioned with an upward bend. On Vanagon and Camper models check that the drain hose is not kinked at the "D" pillar. On Campers also check that the hoses are not kinked as they pass through the cabinets. * An oversized fiber hose can cause the front of the drain pan to rise forcing the water to move to the rear of the pan. * Loose drain hoses at drain pan or elbow (on earlier Waterboxer Campers) connections. If leaks occur at a connection and the hose is not damaged, install a clamp to seal the hose. * Warped drain pans. When replacing the drain pan remove the parts labels to avoid later drainage problems. * In extreme cases, with a high blower speed, water may circulate into a gap where the drain pan and evaporator converge. Seal gap with duct tape (A/C wrap). ****************************************************************** * CAUTION * * Part numbers are for reference only. Always check with your * * Parts Department for latest information. * ****************************************************************** ======================================================================= from Service Bulletins, Model Year 1990 ....................................................................... Technical Bulletin Group: 90 Number: 90-01 Date: Nov 30, 1990 Subject: Speedometer Noisy Model(s): Vanagon, except Syncro Condition: Noise in the magnet shaft bearing of the speedometer. Production: Speedometers with a spring loaded magnet shaft bearing are in production as of: 4.90 VIN 25 LH 071 889 Service Solution: Replace speedometer (No change in part number). Parts Division supply only new version speedometers, which can be identified by the graphite (dark gray) speedometer bushing. (Previously black) Replacing speedometer cable: As of VIN 25 HH 040 185, the protective sleeve is lengthened, eliminating the fastening marking. Note To ensure correct installation, be sure to measure and mark the distance "a" from end of cable to position the securing clip. Distance between end of cable to the mark is 740 mm. (29 in.) 1 2 3 __________ _____________||_||_____ :=|=========|_________/ /______________||_||_____ ^ || || | (_O_) | ^ | | || 90-789 ====================================================================== from Service Bulletins, Model Year 1990 ...................................................................... Technical Bulletin Group: 90 Number: 90-02 Date: Nov 30, 1990 Subject: Instrument Indicator Lights Malfunction Model(s): Vanagon Condition: Instrument cluster warning lights are inoperative at times due to poor contact in the 14 pin instrument plug. The following warning lights may be involved: Oil pressure, alternator, turn signal, high beam, or coolant temperature. Service Solution: Check compact plug for proper contact adn seating. Replace spring terminals when necessary. ======================================================================= Technical Bulletin Group: 90 Number: 92-03 Date: February 29, 1992 Subject: Coolant Indicator LED is Flashing at Normal Temperatures Model(s): All Models CONDITION Coolant overheat / low coolant level indicator LED is flashing at normal coolant temperatures. SERVICE Check the coolant indicator LED according to the list below. The following applies IN ADDITION to tests listed in the Service Microfiche. . * refer to appropriate wiring diagram * disconnect coolant level sensor electrical connector * check coolant level in coolant reservoir *** MUST be between MIN and MAX marks * set digital multimeter, Fluke 83 (US 1119) to ohms function * check resistance of level sensor with digital multimeter Fluke 83 (US 1119) *** must be between 31K Ohm and 65K Ohm with correct COOLANT LEVEL AND COOLANT CONCENTRATION. NOTE If coolant resistance is NOT within the above specifications, the coolant MUST be drained and replaced with NEW coolant mixture of 50 percent water and 50 percent phosphate free coolant antifreeze, Part No. ZVW 237 104. (In Canada, use Part No. G 001 100). The mixing should be performed before filling vehicle cooling system. ***************************************************************** * CAUTION * * Coolant concentrations of 60 percent or higher will cause the * * overtemp / low coolant LED to activate. * **************************************************************** ***************************************************************** * CAUTION * * Coolant antifreeze MUST NOT be reused. Properly dispose of * * used coolant. * **************************************************************** * reconnect sensor connector * check coolant level control unit using wiring diagram NOTE The control unit is located on top of the fuse/relay panel on vehicles up to 1989 model year and thereafter it is integrated into the multi- processor of the instrument cluster circuit board. * if wiring, coolant level sensor and coolant concentration are OK, replace coolant level control unit or instrument cluster circuit board * refer to appropriate Service Microfiche Group 90 - Coolant Temperature Gauge, checking and troubleshooting * confirm proper operation of temperature gauge and blinking LED per Service Microfiche Group 90 ***************************************************************** * CAUTION * * Part Numbers are for reference only. Always check with your * * Parts Department for latest parts information. * **************************************************************** ======================================================================== Technical Information Group: 90 Number: 87-03 Date: July 31, 1987 Subject: Coolant Temperature Gauge Light flashes intermittently / continuously Model(s): All Models, all Model Years Flashing coolant temperature light may be caused by: - Low coolant level. - Coolant level indicator. - Electrical connections on gauge. * Check coolant level, top up if necessary. * Check coolant level sensor for continuity. * Check for loose connection of wiring at terminal 14 connectors of instrument cluster, nuts of temperature gauge, ground connection to body and engine ground. Repair if necessary. If temperature gauge light still flashes: * Replace low coolant level control unit ======================================================================= from Service Bulletins, Model Year 1990 ...................................................................... Technical Information Group: 24 Number: 90-03 Date: March 31, 1990 Subject: Throttle Body - replacement Model(s): Vanagon, all w/ Digijet Injection Replacement throttle body, Part No. 025 133 061B, has been updated with the current throttle switch and lacks one vacuum line for the distributor. When installing this current replacement throttle body, the following mechanical and electrical modifications must be completed. Work Sequence Mechanical: * cut hose "A" (from throttle body to fuel pressure regulator) 150mm from intake air distributor port * install vacuum "T", Part No. 025 201 943, at location "B" (cut in hose "A") * install vacuum hose "C" (from "T" to distributor) (Part No. N 020 353 5, approx. 70mm) between vacuum tee "B" and distributor vacuum advance unit Electrical: * remove the jumper wire for both switches and install supplied connectors. Check for vacuum leaks, check and reset basic engine specifications. ======================================================================= from Service Bulletins, Model Year 1989 ....................................................................... Technical Bulletin Group: 30 Number: 89-01 Date: February 28, 1989 Subject: Clutch Disc, installing Model(s): Vanagon, all with Manual Transmission The clutch disc hub and matching splines of the mainshaft are not to be lubricated with MOS2 grease as described in the repair manual. Instead, lubricate with grean P/N: G 000 100. * splines must be cleaned of all dirt and corrosion before lubricating. * use only a thin coat of grease. * clutch disc must move easily on shaft. ======================================================================= from Service Bulletins, Model Year 1989 ....................................................................... Technical Bulletin Group: 34 Number: 89-03 Date: February 28, 1989 Subject: Revised shift lever bearing Model(s): Vanagon, all with Manual Transmission * Beginning with 06/88 production, the centering holes (arrow) in the shift lever bearing have been deleted. Revised shift lever bearing, adjusting: * loosen nuts (not shown). * turn shift lever bearing to right or left until mounting studs contact ends of slots in bearing (arrows) * tighten nuts to 10 Nm (7 ft lb) Further adjustment of the gearshift lever is to be conducted as described in the repair manual. Note The revised shift lever bearing can be installed in vehicles beginning with 10/82 production. ======================================================================= Product Circular Group: 90 Number: 86-02 Date: July 11, 1986 Subject: Non-interchangeable cigarette lighters Part Identifier: 9062 Model(s): Vanagon Two different cigarette lighters are used in Volkswagen vehicles and they are NOT interchangeable. If installed in the wrong vehicle, it is possible that the lighter will not release properly, thus causing a possible safety hazard. Fig. 1 Fig. 2 Part number 175.919.307B Part number 171 919 305 or 191 919 305 Application: Rabbit - all Application: Cabriolet - all Pickup - all Jetta - all Golf - all Quantum - all GTI - all Scirocco - all Vanagon - all ======================================================================= from Service Bulletins, Model Year 1987 ....................................................................... Technical Information Group: 97 Number: 87-05 Date: July 31, 1987 Subject: Engine cranks too slowly or won't crank - battery cable Model(s): Water-cooled Vanagon, all Model Years A slow or non-cranking engine condition could be caused by high resistance between the starter motor and battery: * Check that the battery is fully charged. * Check the ground connections and battery terminals for tightness and corrosion. Clean and tighten as necessary. If the conditon still exists: * Install a new starter cable or larger diameter, Part Number 251 971 228G. * Install an extra ground strap from the transmission to the body. ....................................................................... Technical Bulletin Group: 27 Number: 87-04 Date: August 06, 1987 Subject: Alternator mounting bolt loose/broken Model(s): Water-Cooled Vanagon Diesel, Vanagon through model year 1985 To prevent the alternator bolt from becoming loose and breaking, the torque specification has been increased. The increased torque specification requires use of a new bolt on 1.9L water cooled engines. To repair a loose/broken bolt: 1.9L Gas Engine * Install new bolt, Part Number N 014 400 4. Torque to 25Nm (18 ft. lb.). Diesel Engine * Replace bolt only if damaged, Part Number is unchanged. Torque to 28-33Nm (21-24 ft. lb.). ======================================================================== from Service Bulletins, Model Year 1987 ........................................................................ Technical Bulletin Group: 17 Number: 87-04 Date: September 30, 1987 Subject: Oil leak from rear - oil pump gaskets Model(s): Vanagon, 1983-1985 Supercedes 87-01, July 15, 1987. Oil seepage from the oil pump on 1.9L water-cooled engines is caused by gaskets which are not fully compressed. * Replace the oil pump gasket with Part Number 025 115 111 (quantity of 2). These gaskets are interchangeable. ======================================================================== from Service Bulletins, Model Year 1987 ....................................................................... Tech News 87-N02 Issue 2, February 1987 Cold Feet, Hot Tip A slight "internal" compression leak into the coolant system of a water- cooled Vanagon is not always easily diagnosed. But what your customer tells your Service Advisor may be very helpful to pinpoint such a problem: * Temperature gauge needle moves into the red * Very little or no heat output * Coolant refill tank overflows * Air in the coolant system If one or a combination of these symptoms apply, be suspicious of a compression leak between cylinder sleeve and cylinder head. Either the metal sealing ring (1) or the 'O' ring (2), or both may be damaged. ....................................................................... (1) is the outer most sealing ring; next to the cylinder head. (2) is the inner most sealing ring; next to the cylinder sleeve. ======================================================================= Import Service, Feb 91, Vol 4, No 2 Subject: Wasserboxer torque spec update "The cylinder head nut torque specification listed in our November 1990 "Wasserboxer" article [the one on the net] has been updated. VW recently increased the recommended head nut tightening torque for all water cooled Vanagon engines to 50 Nm, up from the original specification of 35 Nm. The tightening procedure described in the article must still be followed, substituting 50 Nm for the final torque. We apologize for any problems this specification change may have caused." From: "Dan Houg" ======================================================================= from Service Bulletins, Model Year 1987 ....................................................................... Tech News 87-N04 Issue 4, April 1987 Vanagon Surging/Stalling A customer complaint of surging/stalling on 1986 and '87 Vanagons could be the result of a misadjusted idle/full throttle switch. The digifant system uses a single throttle switch to signal the E.C.U. when the throttle plate is in the fully closed (idle) or fully open (full load) position. Correct adjustment of the throttle switch is very important. If switch is misadjusted, the engine may surge at idle or cut out at steady driving or light acceleration. Here are some key points to remember: * Set or check the switch adjustment only after the engine reaches operating temperature. * When setting or checking your adjustment allow the throttle to return "normally". Do not "snap" the throttle causing it to slam shut ... this could adversely affect the switch adjustment. See the Vanagon Repair Microfiche for complete throttle switch adjustment details. ======================================================================= from Service Bulletins, Model Year 1987 ....................................................................... Tech News 87-N05 Issue 5, May 1987 Easy Does It When removing the cross-over water pipe on a 1982 through 1985 model 1.9 liter Vanagon waterboxer engine ... you have to use care. The cross-over pipe is secured to a welded stud on the intake manifold (arrow) that could break or crack. If this happens, a vacuum leak could develop that would be hard to detect. Such a vacuum leak could cause poor performance under all running conditions due to leaning out of the mixture ... and would occur even when all other systems are go. ======================================================================= from Service Bulletins, Model Year 1987 ....................................................................... Tech News 87-N06 Issue 6, August 1987 Vanagon "Dust Buster" Air Filter Vanagon owners who operate their vehicles in high dust concentration areas have some relief in store ... from our parts store, that is. A specially designed air filter, Part No. 025 129 620 B, standard equipment on Vanagon Syncro models, is what these owners need. Special "dust buster" style air filters are also available for other Volkswagen models that operate in the dust. So if you encounter an air cleaner that looks like a "dust bowl" ... you know what to recommend. ======================================================================= from Service Bulletins, Model Year 1987 ....................................................................... Tech News 87-N08 Issue 8, August 1987 Basic Digifant Assumptions The Digifant engine management system found on late model Vanagons operates on the assumption that basic engine TIMING, IDLE SPEED, THROTTLE SWITCH AND CO%, are correctly set or adjusted. If not, the system will try to compensate for anyu deviation and end up "fighting" with itself to make the engine run. That's why it is critical that these basic engine settings are checked prior to any work you perform on the Digifant system. Equally critical is the need to use Adapter VW 1473 with your VAG 1367 and US 1119 milliamp meter with VW 1315A/2 adapter as well as your CO Meter to verify that idle RPM/ stabilizer milliamp and CO% readings are right. These settings, as well as everything you ever wanted to know about Digifant, are found in the newly released Vanagon Fuel System Pro- Training booklet ... available at your dealership now. For troubleshooting wiring problems, always use the latest wiring diagram which appears on a circular. ======================================================================= from Service Bulletins, Model Year 1988 ....................................................................... Tech News 88-N07 Volume 2, Issue 7, August 1988 Coolant Loop If you have to remove the transmission only on a 2.1 liter Vanagon, be very careful to check the "Coolant Loop" around the engine compartment. You can easily break this loop! Keep an eye on the hose between the engine and the loop. Make sure that the loop does not start to pull tight as teh back of the engine comes down or it will probably break. If this hose seems too short, take it off the loop or loosen the loop from the edge of the engine compartment. ======================================================================= Import Service, March '90 Vol3, No 3 Vanagon coolant leakage "A damaged plastic coolant return flange located at the rear of the right cylinder head can cause coolant leakage on 86-88 models. The plastic flange is close to the engine's drive belts and can be damaged by a loose or broken belt. Engine orverheating can also warp the sealing surface of the flange, causing coolant leakage and more overheating. To correct (or avoid) these problems, replace the damaged plastic flange with a metal coolant return flange, P/N 025 121 160 D, and gasket P/N N 901 685 01." From: "Dan Houg" ======================================================================= from Service Bulletins, Model Year 1990 ....................................................................... Technical Bulletin Group: 20 Number: 20-90 T01 Date: May 31, 1990 Subject: Improved fuel additive ZVW 239 003 Model(s): All Gasoline Engine Vehicles Research by Volkswagen AG and other manufacturers has shown that the performance of todays gasoline engines is directly influenced by the type and quality of fuel used. Fuel without the proper additives can cause deposits to collect on fuel injectors, intake ports and valves. This build-up of deposits can cause the following conditions: * unstable idle * power loss * surging * engine run-on * misfiring * pinging/knocking Extent of deposit build-up varies depending on type of fuel used, operating condition, etc. Refer to current Technical Information Circulars for description of deposit grading system. PREVENTION Prevent deposit build-up through the use of gasolines with injector and intake valve deposit control additives. Consult the suppliers and service stations in your area about fuel grades and additives that prevents or removes these two deposits. In areas where gasoline containing deposit control additives are unavailable, light deposits can be controlled as follows: * add one 6.5 oz. bottle of Autobahn Gasoline Additive, P/N: ZVW 239 003. Note: Fill fuel tank completely. Do not refill until fuel gauge reads 1/4 tank or less. REMOVAL Moderate to heavy deposits can also be removed with Autobahn Gasoline Additive, P/N: ZVW 239 003. When used as follows this additive has shown to be effective. * Check fuel injector spray pattern. Purge injection system with G-16 cleaner. Refer to current Technical Information Circulars for injection purge instructions. * Check that fuel and ignition systems are within specifications. * Add three (3) 6.5 oz bottles of Autobahn Gasoline Additive, P/N: ZVW 239 003 for each of three (3) consecutive fill-ups or 1000 miles. Heavy deposit concentration may require 2 or 3 cycles of the above treatment. Note: Fill fuel tank completely. Do not refill until fuel gauge reads 1/4 tank or less. * Deposit removal with Autobahn Gasoline Additive, P/N: ZVW 239 003 is more efficient with engine at operating temperature and at moderate speed, short distance driving conditions. * Because of possible contamination of the oil, the filter and oil must be changed at the conclusion of each removal cycle. ======================================================================= Technical Information Group: 20 Number: 90-02 Date: March 31, 1990 Subject: Gasoline containg detergents Model(s): All Vehicles with fuel injection Volkswagen United States, Inc. recommends the use of gasolines which contain detergents to keep intake valves and fuel injectors free of deposits. Gasolines without detergents tend to clog fuel injectors and leave residue on intake valves which can cause unstable idle, surging, misfiring of sparkplugs, stlling and rough engine performance in vehicles with fuel injection systems. Because many of our customers may not know whether or not a particular brand of gasoline contains these detergents, we have examined advertising literature published by gasoline refiners and other publicly available literature discussing gasoline ingredients. We cannot independently confirm the accuracy of gasoline advertising claims. The brands of gasolines listed below are claimed by their manufacturers to contain detergent packages designed to keep intake valves and fuel injectors clean. There may be other manufacturers that offer similar detergent packages. Please pass this information on to customers who have experienced driveability problems that may be caused by carbon deposits on intake valves or fuel injectors. Amoco: All grades Arco: All grades Chevron: All grades Citgo: Some grades in early 1990 Conoco: Some grades in early 1990 Diamond Shamrock: Premium grade only Exxon: All grades Fina: All grades in early 1990 Hess: All grades in early 1990 Marathon: All grades Mobil: All grades Phillips 66: All grades in early 1990 Shell: All grades Sunoco: Premium grade only Texaco: All grades Unocal: All grades Hess: All grades in early 1990 Hess: All grades in early 1990 ======================================================================= from Service Bulletins, Model Year 1990 ....................................................................... Technical Bulletin Group: 00 Number: 90-01 Date: August 31, 1990 Subject: Lubricant Capacities/Lubricant Type Model(s): Air-cooled, Water-cooled -- All 1975-1990 Vehicle: Vanagon Model Year: 1980-up - - - - - - - - - - - - - - - - - - - - - - - - - - - - - - - - - - - - Engine Oil: Air-Cooled: 3.0 liter (3.2 quart) 3.5 liter (3.7 quart)/Filter Water-Cooled: 3.8 liter (4.2 quart) Thru 1986 MY 4.2 liter (4.7 quart)/Filter From 1987 MY 4.3 liter (4.8 quart)/Filter Diesel: 3.5 liter (3.7 quart) 3.8 liter (4.2 quart)/Filter Use 'API SERVICE SF' for Gasoline engines. Use 'API SERVICE CC or CD' for Diesel engines. Note: Refer to Owner's Manual for oil grade/climate requirements - - - - - - - - - - - - - - - - - - - - - - - - - - - - - - - - - - - - Manual Transmission: Air-Cooled: 4 speed: 2.9 liter (3.2 quart) SAE 80/80W/90, MIL-L-2105, API/GL-4 Water-Cooled: 4 speed: 2.5 liter (2.8 quart) SAE 80/80W/90, MIL-L-2105, API/GL-4 Diesel: 4 speed: 2.5 liter (2.8 quart) 5 speed: 3.4 liter (3.8 quart) SAE 80/80W/90, MIL-L-2105, API/GL-4 - - - - - - - - - - - - - - - - - - - - - - - - - - - - - - - - - - - - Automatic Transmission: All Models: Dry Fill: 6.0 liter (6.3 quart) ATF Dexron/Dexron II Refill: 3.0 liter (3.2 quart) ATF Dexron/Dexron II Automatic Differential: All Models: 1.2 liter (1.3 quart) SAE 90W, MIL-L-2105 B, API/GL-5 - - - - - - - - - - - - - - - - - - - - - - - - - - - - - - - - - - - - Cooling System: Waterboxer & Thru 1986 MY 15.2 liter (16.9 quart) Diesel Waterboxer From 1987 MY 16.7 liter (18.6 quart) Use only Phosphate Free Coolant ZVW 237 104 (G11) or equivalent - - - - - - - - - - - - - - - - - - - - - - - - - - - - - - - - - - - - Power Steering: All Models: 1.2 liter (1.3 quart) ATF Dexron II - - - - - - - - - - - - - - - - - - - - - - - - - - - - - - - - - - - - Windshield Washer Solvent: All Models: Front: 3.9 liter (4.3 quart) 9.0 liter (9.5 quart) w/ headlite washers Rear: 1.0 liter (1.1 quart) Recommended Solvent: Concentrated ZVW 177 901/903 Pre-mix ZVW 177 902 or Equivalent - - - - - - - - - - - - - - - - - - - - - - - - - - - - - - - - - - - - Air Conditioning: Air-Cooled & Water-Cooled: Refrigerant (R-12) - 1190 + 85 grams (42.0 + 3.0 oz.) Refrigerant Oil - 135 cc (4.75 oz.) Diesel, From 1986 MY: Refrigerant (R-12) - 1438 grams (50.75 oz) Refrigerant Oil - 237 cc (8.0 oz.) U.S.A. Only: Use any domestic available refrigerant oil Canada Only: Use Suniso 5GS refrigerant oil, available through VWC, Part No. X 091050 ********************************************************************** * CAUTION: Part numbers are for reference only. Always check with * * your Volkswagen Parts Department for latest information. * ********************************************************************** ======================================================================= from Service Bulletins, Model Year 1988 ....................................................................... Technical Information Group: 40 Number: 88-01 Date: May 31, 1988 Subject: Upper control arm bushings, checking Model(s): Vangon, all model years An insufficient seal at the outer ends of the upper control arm bushings can cause premature wear to the bushings. Visually inspect the bushings as follows to determine if replacement is necessary. NOTE When checking the bushings, both front wheels must be on the ground. * Bolt head or nut/washer must be postioned in center of bonded rubber bushing. * If bolt head or nut/washer comes in contact with supporting ring (arrow), wear limit has been reached and bushing must be replaced. this same information is also shown on page 40.5a of the July 15, 1991 edition of the Bentley Vanagon Manual. ======================================================================= from Service Bulletins, Model Year 1991 ....................................................................... Technical Information Group: 68 Number: 91-02 Date: April 30, 1991 Subject: Automatic Rear 3-Point Seat Belts, Retrofit Installation Model(s): Vanagon, 1980-1989 Model Years Vanagon Camper/Multivan (right rear only), 1980-1989 Model Years AUTOMATIC REAR 3-POINT SEAT BELTS, RETROFIT INSTALLATION ********************************************************************** * CAUTION * * Part numbers are for reference only. Always check with your Parts * * Department for latest information. * ********************************************************************** PARTS REQUIRED Part Number Description Quantity ------------ ----------------------------------- -------- 253 857 815D Rear 3-point seat belt (left side) 1 253 857 816D Rear 3-point seat belt (right side) 1 NOTE Check with your Parts Department for additional installation parts. Not all parts listed may be applicable to all vehicles. * remove rear seat bottom * remove existing 2-point left/right side lap belt * remove rear floor carpet * remove right rear luggage area trim panel * mark and cut rear luggage area trim panel using dimensions as shown on Page 3 * locate, by feel, threaded hole under D-pillar trim (arrow) * cut hole in trim to expose threaded bolt hole * using bolts (2), mount retractor assembly (1), to side panel (3) -> 40 Nm (30 ft lb) * install belt through cut hole in trim panel * mount upper belt guide onto D-pillar -> 40 NM (30 ft lb) * install belt anchor (arrow) to original lap belt anchor point -> 40 Nm (30 ft lb) * reinstall right rear luggage area trim panel * repeat procedure for left side belt assembly, noting to reverse dimensions accordingly * reinstall all other components in reverse order * check rear 3-point belts for proper function --------------------------------------------------- Automatic rear 3-point | | | | seat belts, retrofit | | | | installation | Diag. | | Quality | (one side only) | Check | Repair | Check | --------------------------------------------------- Labor Op. 6876312 | -- | 120 T.U.| -- | --------------------------------------------------- DIAGRAM (8-1/4in) \ / ______ ________ \ / 38mm | hole | (15-7/8in) \ / ______ |______| \ / | / || | / | (5-7/8in)| | / |----------|-- | / | | 32mm (1-1/4in) ______| /---------------------------------| |---------------| || ........................................ end ........................... that is, the dimensions of the hole are 71mm x 38mm (2-13/16in x 1-1/2in). but the front edge of the hole is 203mm (8in) below the top edge of of the luggage area trim panel, while the rear edge of the hole is 210 mm (8-1/4in) from that same edge. the hole is slightly tilted. the notch is cut in the bottom to accomodate those three bolts that hold the retractor assembly to the metal of the body. also notice that this does NOT say anything about those 1986-1989 vanagons with air conditioning. the upper belt guide attachment point will be behind the air conditioning housing that runs vertically over the D-pillar. so you would have to cut a hold in the plastic a/c housing to pass the belt through. (it helps to look at a 1990 or 1991 model, to see how the factory installation looks). in order to prevent damage to the belt, the little plastic edging (that covers the edges of the hole in the a/c housing) will have to be installed. ======================================================================= from Service Bulletins, Model Year 1991 ....................................................................... Technical Information Group: 68 Number: 91-04 Date: April 30, 1991 Subject: Automatic 3-Point Left Center Seat Belt, Retrofit Installation Model(s): All Vanagon w/ center seat, EXCEPT Camper/Multivan 1980-1989 Model Years AUTOMATIC 3-POINT LEFT CENTER SEAT BELT, RETROFIT INSTALLATION ********************************************************************** * CAUTION * * Part numbers are for reference only. Always check with your Parts * * Department for latest information. * ********************************************************************** PARTS REQUIRED Part Number Description Quantity ------------ ----------------------------------- -------- 253 857 811D 3-point seat belt (left side) 1 NOTE Check with your Parts Department for additional installation parts. * remove rear seat back * remove rear seat bottom * remove original left center belt * remove rear left side panel trim * measure location of belt retractor, belt guide, and mounting holes, using dimensions on page 3 * cut panel as required * reinstall trim panel * install seat belt retractor on outside of panel, as shown -> 40 Nm (30 ft lb) -> hand tighten forward bolt only * locate, by feel, threaded hole in C-pillar (arrow) for belt guide D-ring * cut C-Pillar trim from threaded hole, install belt guide D-ring -> 40 Nm (30 ft lb) * install anchor of 3-point belt into forward mounting hole of retractor bracket (arrow A) -> 40 Nm (30 ft lb) * align bracket for betls, reinstall rear seat bottom and belts * reinstall rear seatback * install new buckle for 3-point belt * check seat belt for proper function --------------------------------------------------- Automatic left center | | | | 3-point seat belt, | | | | retrofit installation | Diag. | | Quality | (left side only) | Check | Repair | Check | --------------------------------------------------- Labor Op. 6876311 | -- | 150 T.U.| -- | --------------------------------------------------- DIAGRAM Top Front of Vehicle --> Rear Left side trim panel ------------------------------------------------- | | | | _________ _________________|__________ | 67mm | | 38mm |(2-5/8in)| | (1-1/2in) \ |_________|_________________|_____:________ \ | . \ < 102mm > | . >\ 31mm< hole (4in) | . ---\-- () 22mm __________ _______._ | 442mm . \ . | | . | (17-3/8in) . \ . | 118mm | 327mm | . . \ | (4-5/8in)| (12-7/8in) | . . \ _._|__________|._ . | . . \ . . . | . . \ . . . ()--------.--(hole 22mm) . \ 245mm 216mm . > 31mm|< . (7/8in) 298mm \ (9-5/8in) (8-1/2in) . | . . (11-3/4in) \ . . . | 203mm . . \ . . . | (8-1/8in) . . \ . . . | . . .____________ \_._____________.______.__________| ___._______._ ........................................ end ........................... that is, the dimension of the bottom hole is 118mm x 102mm (4-5/8in x 4in). but the front edge of the hole is 216mm (8-1/2in) above the bottom edge of the trim panel, while the rear edge of the hole is 245mm (9-5/8in) from that same edge. that is, the hole is slightly tilted. the upper hole is 67mm x 38mm (2-5/8in x 1-1/2in) and appears also to be slightly tilted. the upper hole has its bottom front edge 442mm (17-3/8in) from the bottom edge of the trim panel. notice that the instructions do NOT say anything about those two 22mm (7/8in) holes. both are 31mm (1-1/4in) from the closest edge of the trim panel. the lower of the two is 203mm (8-1/8in) from the bottom edge, while the upper of the two holes is 298mm (11-3/4in) above that same bottom edge. i have no idea what those holes are supposed to be used for. ======================================================================== Technical Information Group: 28 Number: 87-04 Date: July 15, 1987 Subject: Rough idle or misfiring during partial load Model(s): All Models, all Model Years A rough idle or misfire during partial load could be caused by ignition sparks jumping from the plug wire connector to the noise suppresion shield, or the cylinder head. * Remove and inspect the plug connector for white spots or burn marks. * On those vehicles equipped with a suppressor shield on the distributor cap, it is necessary to remove the shield and check for white spots or burn marks on the distributor cap. if white spots or burn marks are present, replace the damaged components. ======================================================================== 135 1968-1979 Buses Removing and Installing Fuel Tank Sender Unit (from Repair Manual Type 2, Second Edition, VW AG) The sender unit can be removed without taking out the engine, bulkhead and fuel tank. This is done by cutting a hole in the floor plate which is then closed afterwards with a plate available as a spare part. The following parts are required: 1 ea. Cover plate (oval) for floor plate. 1 ea. gasket for cover plate 4 ea. screws B 4.2x9.5, DIN 7981, galvanized - VW Universal Adhesive ********************************************** * WARNING * * DO NOT USE any of the following tools * * to cut the hole or clean edges: * * Gas Torch, Grinding Disc, Parting Disc. * ********************************************** - Disconnect the battery ground cable. - Remove the spare tire and spare tire cover. - Measure the center point of the hole: - from the left (driver) interior side panel, next to the spare tire hole: a = 807mm (31.77 in.) - from the rearmost edge of the rear hatch opening (the metal 'rim', that is next to the rubber gasket for the rear hatch): b = 893mm (35.15 in.) - See Fig. 1 - Cut hole and remove burrs. - radius of hole is: r = 40mm (1.57 in.) - width of cut is: w = 70mm (2.75 in.) - See Fig. 2 - Cut into the rib at front and rear edge of hole about 15mm (0.59 in.) and hammer rib flat. Support metal from underneath with a strong lever. - Check that the plate and seat fit properly. To ensure that the plate seals properly, the hole should be lifted slightly around the edge. - Place the cover over the hole, mark off the screw hole positions on the floor plate and drill 3mm (1/8 in.) diameter holes for the four screws. - Renew fuel guage sender unit. - Connect up the battery ground strap and check operation of the sender unit. - Stick seal to plate and secure plate with four taping screws. Fig. 1 ---------------------------------------------------------------- (rear of bus) latch ====================----==================== : | a = 807mm : |-----|| 31.77 in. : | || : |spare|| b = 893mm : |tire || 35.15 in. b |hole || : | || : | || : | || : | || : |-----|| : | x | forward edge > . . . . . . . . . . . . . . . . . . of engine ledge (dropoff to floor of bus) Fig. 2 ---------------------------------------------------------------- (rear of bus) raised ribs-> || || || || || a = 807mm (31.77 in.) on engine || || || || || r = 40mm (1.57 in.) ledge || || || || || w = 70mm (2.75 in.) || || : /---- › || || | || || w (-r-x<--)------------a--------------->| || || : ›-----/ || || forward edge > . . .|| . . ||. . .|| . . ||. . . . of engine ledge (dropoff to floor of bus) description of hole: at the measured point x (a from the side, and b from the rear edge), draw a circle of radius r. on the front-rear axis of the circle, truncate the circle to 35mm in front of x and 35mm to the rear of x (so the hole will look like a flattened circle). the forward edge of the hole will almost be at the dropoff ledge from the engine compartment to the floor of the middle of the bus. ----------------------------------------------------------------------- one of the raised ribs on the engine compartment will be just right (passenger side) of the point x. this is the one that will have to be cut and flattened. the picture shows a flat wrecking bar type instrument being held under the cut rib, while the rib is being flattend with a small tack hammer. ----------------------------------------------------------------------- the next picture shows the edges of the hole having been curled upward just a bit (with pliers, i assume. or with one of those 'lip' maker tools that body shops used to use). ----------------------------------------------------------------------- comments: even though the cover plate is listed as 'no longer available', i suppose you could make your own plate. it would just need to have a small downward lip around the outer edge ... to secure and seal the gasket in place. the four screw holes were basically laid out 2 per side of the hole, like so: /--------› / o o › ( x ) where x is the center-point of the hole › o o / ›--------/ ========================================================================= Import Service, Dec '90, Vol 3, No 12 Subject: VW rotor govenor "A faulty distributor rotor may cause the engine to cut out on some 69 to 71 VW Type 1, 2, and 4 vehicles. the rotor has a built in centrifugal govenor cutout that prevents the engine from over-revving. Low speed cutout may be caused by a weak govenor spring. the rotor can be replaced with a conventional non-governor rotor, but the engine may be damaged by over-revving." From: "Dan Houg" Import Service, March 1995 Vol 8, No 3 Reader 'tech tip' submission "If you have low cranking compression but little cylinder leakdown on an air-cooled VW engine equipped with hydraulic valves, try readjusting the valves. If this does not correct the problem, I have seen several cases where the hydraulic lifters were bad enough to hold the valves open slightly at all times. The defective hydraulic lifters can be replaced without removing the engine or cylinder heads, which will save your customer quite a bit of money. Dan Rickert Almanor Import Repair Clear Creek, California" From: "Dan Houg" ========================================================================= Import Service, March 1995 Vol 8 No 3 Reader 'tech tip' submission: "If you have done some brake work on a VW Vanagon that requires you to bleed the system, you will find the master cylinder behind the instrument cluster. Because of this fact, it is hard to get a power brake bleeder attached to the cylinder. I have found that a screw on radiator cap fitting from a cooling system pressure testing outfit will fit the threads on the brake master cylinder reservoir. Use the cap fitting to pressurize the brake system, then proceed to bleed the brakes solo. Al Tuck Repair Dynamics Steamboat, Colorado" Dan's Note: Great idea here folks! BUT make sure the cap you use is new or ABSOLUTELY dry as any residual moisture left from its cooling system application will be forced into the brake system. I have a 'spare' bad cap that will work for this so i'll have to give it a try sometime. From: "Dan Houg"